
Kal Plastics
Plastics, 2050 E 48th St, Los Angeles, California, 90058, United States, 11-50 Employees
Phone Number: 32********
Who is KAL PLASTICS
Kal Plastics manufactures an extensive assortment of high-quality material handling containers for a wide variety of applications: Available in prime virgin, post-industrial or post-consu...
Read More
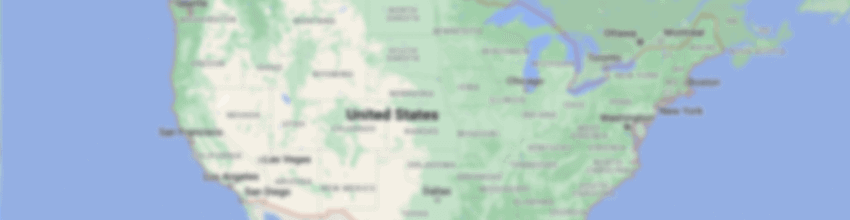
-
Headquarters: 2050 E 48th St, Los Angeles, California, 90058, United States
-
Employees: 11-50
-
Revenue: $10 Million to $25 Million
-
CEO: Juliet Goff
Does something look wrong? Fix it. | View contact records from KAL PLASTICS
Kal Plastics Org Chart and Mapping
Sign in to CIENCE GO Data to uncover contact details
Free credits every month
Frequently Asked Questions Regarding Kal Plastics
Answer: Kal Plastics's headquarters are located at 2050 E 48th St, Los Angeles, California, 90058, United States
Answer: Kal Plastics's phone number is 32********
Answer: Kal Plastics's official website is https://kal-plastics.com
Answer: Kal Plastics's revenue is $10 Million to $25 Million
Answer: Kal Plastics's SIC: 3089
Answer: Kal Plastics's NAICS: 326199
Answer: Kal Plastics has 11-50 employees
Answer: Kal Plastics is in Plastics
Answer: Kal Plastics contact info: Phone number: 32******** Website: https://kal-plastics.com
Answer: Kal Plastics manufactures an extensive assortment of high-quality material handling containers for a wide variety of applications: Available in prime virgin, post-industrial or post-consumer materials. Kal Plastics can help manufacture design and develop product casings for specialized, medium projects.In addition to our vacuum forming expertise, we provide a wide range of secondary operations, including, but not limited to: Die Cutting, Pop Riveting, Drilling, Hot Stampling, Pad Printing, Fabrication, Precision 5-Axis CNC trimming/finishing. Vacuum forming offers processing advantages over competitive processes such as fabrication, blow molding, injection blow molding, rotational molding, and injection molding. Because tooling costs are lower, relatively large parts can be economically fabricated. Vacuum forming is also ideal for prototyping and product development due to the lower tooling costs and faster turn around. In many instances, a vacuum formed part is of higher quality and will last longer than an identical part made by a different process. This is especially true when comparing an injected molded part to the same part, vacuum formed. Vacuum forming is also ideal for any part not expected to exceed a volume of 50,000 or more.
Answer:
Premium Sales Data for Prospecting
-
Sales data across over 200M records
-
Up-to-date records (less decayed data)
-
Accurate Email Lists (real-world tested)
-
Powerful search engine and intuitive interface
Sign in to CIENCE GO Data to uncover contact details
Free credits every month